Plant governance: AI platform for Volteco


Founded in 1976, Volteco is a leader in the waterproof technology sector. Always looking for innovation and improvement, the Company offers leading products capable of sustaining construction companies in the best possible way.
The high-tech plant boasts automated processes and a technical/scientific pool focused on the use of materials, innovative solutions and products with low environmental impact.
CUSTOMER NEEDS
After years of research and development, Volteco has launched the production of Amphibia, a water-reactive waterproofing membrane, unique in the world for its technical characteristics and ideal for use in waterproofing buildings. The production site, a unique prototype in the world, is equipped with hundreds of sensors useful for controlling the physical, chemical and mechanical processes to which the raw materials are subjected (pressures, temperatures, torques, speeds, etc … ) .
Such a complex context made it difficult to understand where to intervene in order to govern the production process, control the final quality of the product and reduce waste.
Volteco was looking for a solution capable of reducing the rate of defects and waste in the production line of hydro-reactive membranes.
At the same time, the Company needed to implement a system that would be able to anticipate failures and system malfunctions so as to increase the availability of the line itself.
Following a period of analysis of the entire process, beanTech proposed RealSIGHT, an Industrial IoT solution capable of digitizing the entire process of the production line.
RealSiGHT has brought multiple advantages to Volteco, verifiable and measurable in terms of quantitative and qualitative production performance involving:
- Increased technological knowledge of the entire process;
- Greater understanding of the correlation between events and process parameters;
- Anticipation of anomalous and/or harmful behaviors for the quality of the product;
- Improved productivity (more pieces in less time and at a lower cost) and quality.
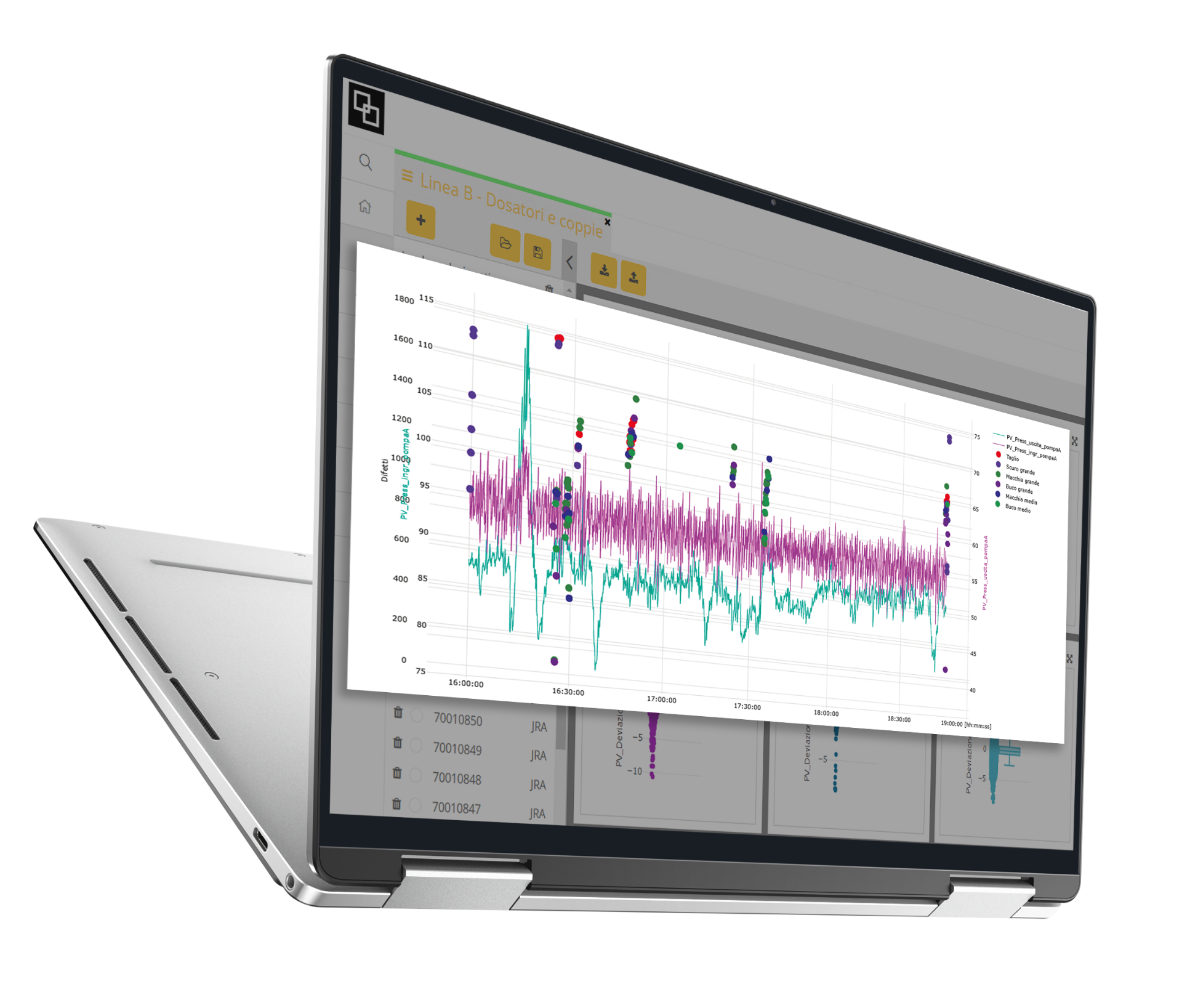
Between March and April 2022 the new ADA system was introduced. The first most significant results after a few months were:
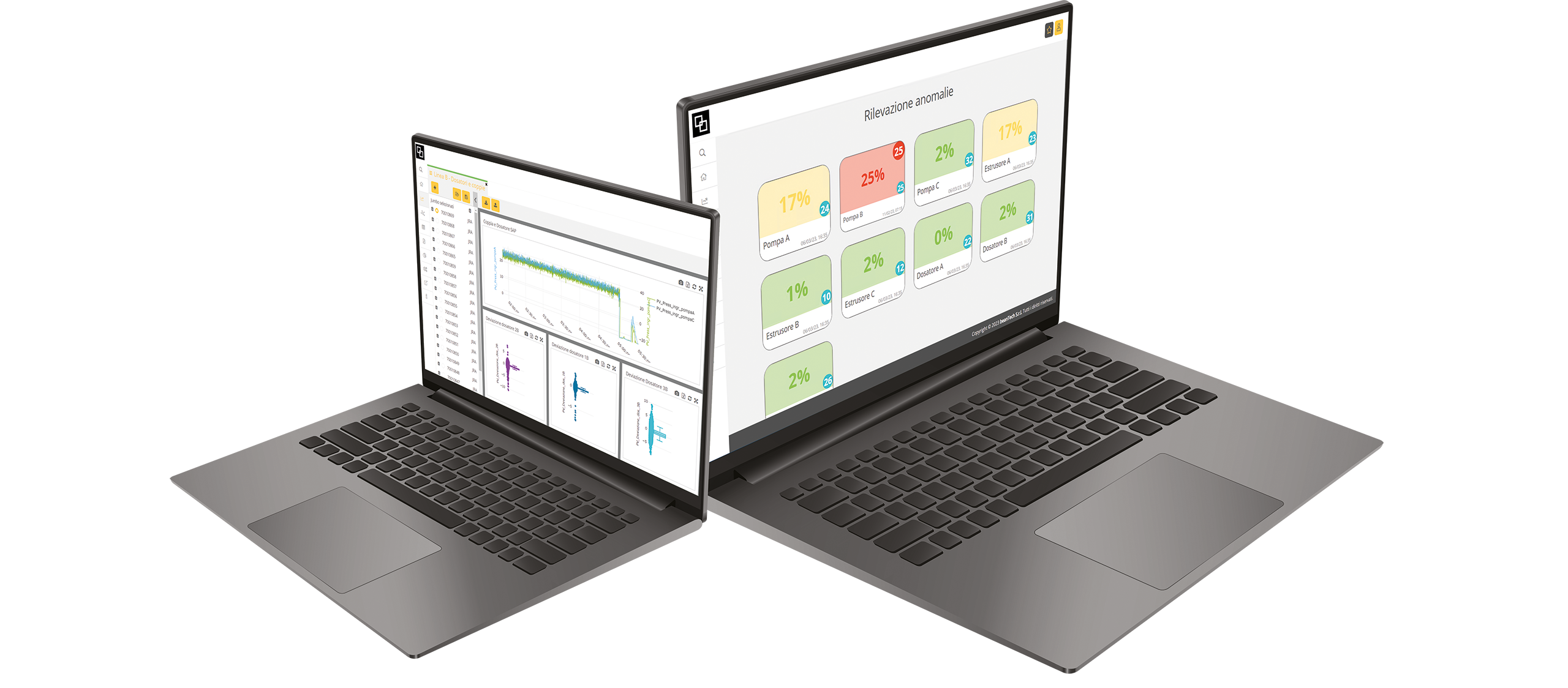
THE SUCCESS STORY AT A CLICK
Don't miss all the details of the Industrial Internet of Things solution created for VOLTECO.
[…] We had to change the paradigm by using all existing information to manage the production process, realizing that new digital technologies would allow us to overcome certain critical issues and greatly accelerate the learning process.
We therefore needed a technological partner capable of grounding these new technologies by adapting them to the complex context, with beanTech we have found a concrete answer and a strategic partner who has been able to accompany us on this path by integrating their skills with ours and creating a plant supervision system which, thanks to the adoption of artificial intelligence algorithms, allows us to understand where to intervene in advance both by checking the final quality of the product and for the maintenance of critical plant components.